Electric Duct Heater
Electric Duct Heater
Electric Duct Heaters are widely used across various buildings and industries for different purposes. These include providing primary heating for fresh air supply in HVAC systems, offering supplemental heating to specific zones or rooms, and heating air supplies for industrial processes. They can also be equipped with features such as thermostats, temperature controls, and "run-on timers" for fan operation.
Electric Duct Heaters come in different shapes and sizes and we offer either rectangular or circular models.
Rectangular Duct Heaters: Rectangular duct heaters, with capacities reaching up to 2000 kW, are designed for heating supply air in duct systems, central ventilation units, and industrial processes. When appropriately rated, they can effectively heat entire homes or buildings. Thanks to a versatile production system, these heaters can be precisely tailored to specific applications, whether for air handling units, industrial processes, or demanding environments. Customisation options may include enhanced electrical insulation, stainless steel construction, high power output, or operation under elevated temperatures.
Circular Duct Heaters: Circular electric duct heaters are designed to heat ventilation air supplied to individual rooms or zones with separate temperature controls. In well-designed systems, they can also provide heating for entire buildings. These heaters are commonly used for reheating supply air in ventilation systems with heat recovery. They are available with either built-in electronic regulators or options for external control. All standard models come equipped with an electronic flow monitor as a default feature.
Technical Specifications
Technical Specifications
Single Phase 240/50/1
Duct mm Diameter | Airflow Range (m³/s) | Power Range (kW) |
---|---|---|
100 | 0.01 - 0.05 | 0.4 - 0.6 |
120 | 0.02 - 0.08 | 0.3 - 1.8 |
160 | 0.02 - 0.08 | 0.3 - 2.7 |
200 | 0.03 - 0.15 | 0.6 - 5.4 |
250 | 0.03 - 0.21 | 0.6 - 5.4 |
315 | 0.11 - 0.5 | 0.9 - 5.4 |
400 | 0.18 - 0.9 | 3 - 4 |
3 Phase 400/50/30
Duct mm Diameter | Airflow Range (m³/s) | Power Range (kW) |
---|---|---|
200 | 0.03 - 0.15 | 6 |
250 | 0.05 - 0.21 | 6 - 12 |
315 | 0.11 - 0.5 | 6 - 12 |
400 | 0.18 - 0.9 | 6 - 12 |
Design and Installation
Design and Installation
When installing duct heaters, ensure they are positioned in a straight section of ductwork with sufficient clearance from bends, filters, or fans to allow even airflow. Proper electrical connections should follow the manufacturer's guidelines, including grounding and ensuring the supply voltage matches the heater's requirements. Incorporate safety features like flow monitors, temperature controls, and overload protection to prevent overheating. For industrial or hazardous environments, verify compliance with specific safety standards, such as IP ratings or explosion-proof requirements. Finally, test the system after installation to confirm proper operation and airflow distribution.
Please get in touch if you have any further questions.
Benefits of Electric Duct Heaters vs Gas Burners
Benefits of Electric Duct Heaters vs Gas Burners
Electric process duct heaters often outperform conventional gas burners in several key areas, depending on the application. Here are the main advantages:
1. Energy Efficiency
- Electric Heaters: Highly efficient, with minimal energy loss because nearly all electrical energy is converted to heat.
- Gas Burners: Typically less efficient due to heat losses in combustion and flue gases.
2. Precision and Control
- Electric Heaters: Offer precise temperature control, often down to ±1°F (±0.5°C).
- Gas Burners: Temperature control can be less accurate due to lag in the combustion process and variability in gas flow.
3. Environmental Impact
- Electric Heaters: Emit no direct greenhouse gases, assuming clean energy sources. They can be paired with renewable electricity for a low-carbon footprint.
- Gas Burners: Emit CO₂, NOx, and other pollutants directly during combustion, contributing to environmental harm.
4. Safety
- Electric Heaters: No open flames or combustible fuels, reducing fire and explosion risks.
- Gas Burners: Pose risks from gas leaks, open flames, and incomplete combustion.
5. Maintenance
- Electric Heaters: Have fewer moving parts and no need for combustion-related maintenance like cleaning burners or inspecting flues.
- Gas Burners: Require regular maintenance to clean burners, check fuel lines, and ensure safe operation.
6. Installation and Space
- Electric Heaters: Easier to install, with fewer ventilation and exhaust requirements. Compact designs save space.
- Gas Burners: Require additional infrastructure such as gas supply lines, venting, and exhaust systems, increasing complexity and space requirements.
7. Flexibility
- Electric Heaters: Can operate efficiently at low loads, making them suitable for applications with variable heating demands.
- Gas Burners: Less efficient at low loads and may require additional components to modulate performance.
8. Noise Levels
- Electric Heaters: Operate silently.
- Gas Burners: Produce noise during combustion and operation.
Share
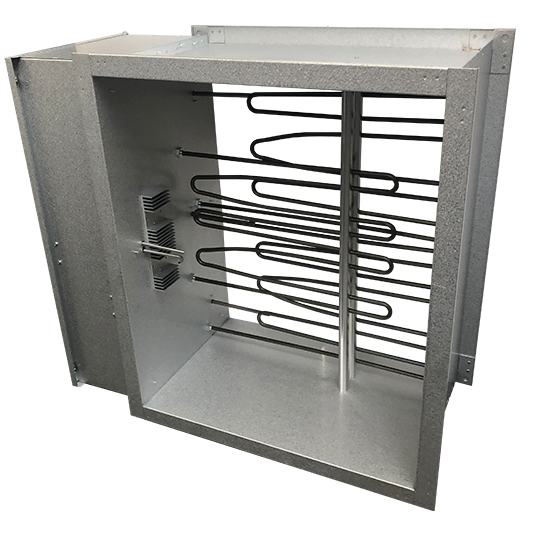
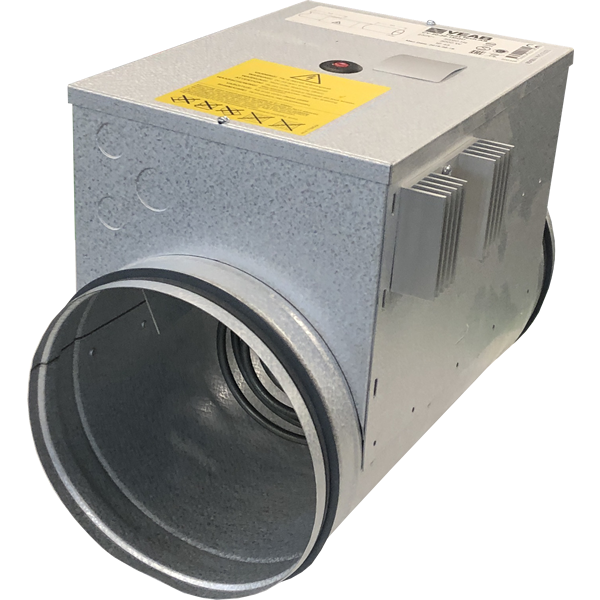
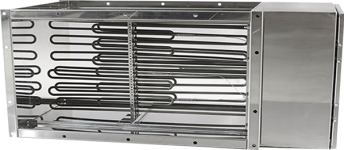